Continuous product improvement¶
Continuous improvement is a general philosophy intended to help individuals and organizations constantly improve themselves and the work they produce.
There are a variety of different methodologies that fall under the umbrella of continuous improvement. These include kaizen, six sigma, and lean, among others. While the specific steps of each method differ, their goal remains the same: implement a process by which improvement is a perpetual goal, rather than a one-time accomplishment.
The sections below contain details about how Odoo can be used to implement four general steps common to many of the most popular continuous improvement strategies, with links to documentation about configuring the necessary features. The final section details how a specific company might configure these Odoo implementations within their organization.
Quan trọng
Continuous improvement is not a one-size-fits-all methodology. While most strategies include between four and six steps, proper implementation requires developing a system tailored to the specific needs of each company.
This is not a limitation, but rather a benefit, as it makes the methodology flexible enough to adapt to almost any use case. Odoo, in particular, adapts well to this flexibility, as it can be configured to meet the needs of almost any workflow.
As such, it is important to remember the content below only provides examples of how Odoo might be used. They should be viewed as more of a starting point, rather than a concrete outline that every organization must follow.
Identify problems¶
Before improvement can begin, it is necessary to determine where improvement is necessary. This is where identifying problems comes into play. Two of the best Odoo apps for identifying problems with products or processes are Helpdesk and Quality.
Hỗ trợ¶
The Helpdesk app is useful for receiving feedback from outside of the organization, like from clients or customers. This is accomplished by implementing one (or more) of the methods for receiving tickets, including email aliases, live chat conversations, and website forms.
Using these methods, customers can submit feedback about problems, which is then reviewed by a member of a helpdesk team. Depending on the outcome of the review, the team member may decide to take further action to ensure the issue is addressed. This can include creating a quality alert.
Chất lượng¶
The Quality app is useful for receiving feedback from within the organization, like from employees.
One method for accomplishing this is to set up a quality control point (QCP). A QCP is used to automatically create quality checks at regular intervals, prompting employees to inspect, and confirm, the quality of a product.
Khi phát hiện vấn đề, nhân viên có thể tạo cảnh báo chất lượng để thông báo cho bộ phận quản lý chất lượng. Cảnh báo chất lượng cũng có thể được tạo độc lập với QCP khi nhân viên phát hiện vấn đề mà không cần được yêu cầu kiểm tra trước. Đây là cách hiệu quả để nhân viên hỗ trợ khách hàng thông báo cho bộ phận chất lượng về các vấn đề được đề cập trong phiếu hỗ trợ khách hàng.
Suggest improvements¶
Once a problem is identified, the next step is to put forward ideas for how to address the problem. As with identifying problems, the Quality app is also useful for suggesting improvements. In addition, the PLM (Product Lifecycle Management) app can be used for this purpose, as well.
Chất lượng¶
When creating a quality alert to bring an issue to the attention of a quality team, the Corrective Actions and Preventive Actions tabs can be used to provide feedback about how the issue can be addressed.
The Corrective Actions tab is used to suggest a method for fixing items affected by the
issue. For example, Screw the bolts on tighter, so the seat stays in place
.
The Preventive Actions tab is used to suggest a method for preventing the issue from
occurring in the future. For example, Do not tighten the screws too much, or they will be
stripped
.
The quality team that reviews the alert sees these suggested actions, and can take them into account when deciding how to address the issue.
QLVĐSP¶
The PLM app is used to manage the lifecycle of a product from its introduction through each successive version. As such, it is useful for testing ideas for product improvements.
Using engineering change orders, product management teams can create new iterations of product BoMs, adding or removing specific components or operations, as needed. The products created using these BoMs are put through a review process to confirm the effectiveness of the changes.
Implement strategies¶
Việc triển khai chiến lược bao gồm thực hiện các giải pháp đã được đề xuất trong bước đề xuất cải tiến. Ứng dụng PLM vẫn tiếp tục hữu ích trong bước này, vì nó có thể được cấu hình để thực hiện các cập nhật BoM. Ứng dụng Dịch vụ hiện trường cũng có thể được một số công ty sử dụng để cải tiến các sản phẩm đã được bán cho khách hàng.
QLVĐSP¶
Once BoM changes have gone through the proper review process, they can be approved, and the updated BoM put into use. This is accomplished by configuring one of the ECO review stages to apply the changes made to the BoM, at which point the updated BoM becomes available for new MOs.
Product BoMs can continue to be updated, as needed. The version control features of the PLM app allow for easy management of all versions of a given BoM.
Dịch vụ hiện trường¶
The PLM app is a great way to make changes to product BoMs. However, these changes only affect products produced using the new BoM. If a defective product has already been sold to a customer, it may be necessary to repair (or update) that product.
In such a case, the Field Service app can be used to schedule onsite interventions. These interventions allow service technicians (or other employees) to be sent to a customer's location to address an issue with a product.
Review actions¶
Reviewing actions is where the "continuous" part of continuous improvement comes into play, as it allows an organization to evaluate the decisions made in the previous steps. As such, this step is, essentially, returning to the beginning of the process, so that additional problems can be identified and addressed.
This means that the Helpdesk and Quality apps should be used again to receive customer and employee feedback. Another app that may be useful at this stage is the Surveys app.
Khảo sát¶
After implementing changes to a product or process, it may be wise to solicit customers for their feedback directly, rather than waiting to hear from them of their own volition. This may bring to light feedback that customers may have otherwise neglected to share.
One of the best ways to accomplish this is through the Surveys app. Creating a survey, and sending it to customers who receive an updated product, increases the likelihood of receiving relevant feedback about the product.
Example workflow: coat rack product improvement
Wood Hut is a manufacturer of fine wood products. They are committed to manufacturing products of the highest-possible quality, and are always looking for ways to improve the products they sell, along with the processes used to create them.
Wood Hut uses the Odoo platform to manage every element of their production, fulfillment, and customer satisfaction processes. They have developed a custom product improvement workflow that incorporates the Helpdesk, Quality, PLM, and Manufacturing apps.
One of Wood Hut's most popular products is their coat rack. It's made entirely of oak, and customers describe it as "sleek and elegant." However, recent customer feedback about the coat rack has brought attention to quality issues that necessitate revising the current manufacturing process.
Quy trình sửa đổi sản phẩm bắt đầu khi bộ phận chăm sóc khách hàng nhận được một phiếu hỗ trợ trong ứng dụng Hỗ trợ từ một khách hàng gặp vấn đề với giá treo áo mà cô ấy đã mua. Khách hàng, Abigail Peterson, phát hiện rằng giá treo áo bị đổ khi treo hơn năm chiếc áo. Đây là một vấn đề nghiêm trọng, vì giá treo áo có đủ chốt để treo sáu chiếc áo.

Marc, the customer service employee assigned to the helpdesk ticket, opens the Quality app, and creates a new quality alert. He tags the Production Quality Team and assigns Julie Andreson as the quality employee responsible for the alert.
Julie reviews the alert, and consults with her team about the best course of action. They decide that it is necessary to revise the product's BoM to prevent the issue from occurring in the future, which Julie notes in the Corrective Actions tab of the quality alert.
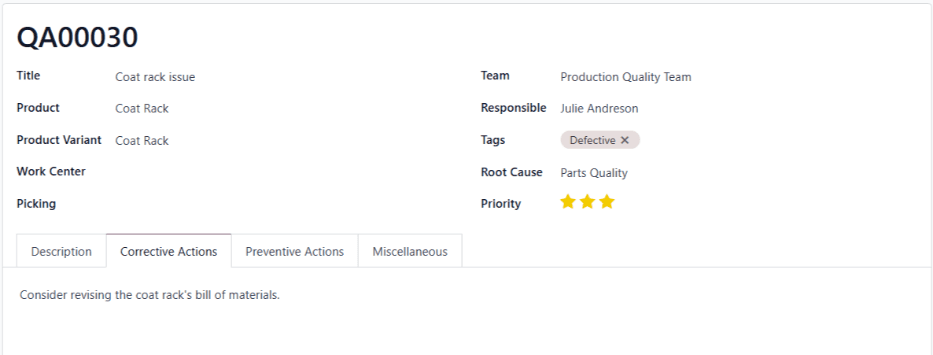
Then, Julie messages product engineer, Joe Kazan in the chatter of the quality alert to bring it to his attention. Joe opens the PLM app and creates a new ECO, noting the problem with the coat rack, and suggesting that a change to the product's BoM may be necessary.

Joe clicks Start Revision, and then the Revision smart button to open version two of the coat rack's BoM. This BoM was created alongside the ECO, and remains archived until it is approved.
Sau một số lần thử nghiệm, Joe phát hiện ra rằng việc thêm một thanh đỡ kim loại vào giá treo áo khoác sẽ giúp tăng cường độ bền, cho phép giá treo giữ được sáu hoặc nhiều áo khoác hơn mà không bị đổ. Anh ấy cập nhật BoM để bao gồm thanh đỡ làm một trong các thành phần và thêm một thao tác bổ sung để đảm bảo nó được lắp đặt trong quá trình sản xuất. Cuối cùng, anh ấy để lại một tin nhắn trong phần trò chuyện của ECO để thông báo cho quản lý của mình, Jose, rằng ECO đã sẵn sàng để xem lại.
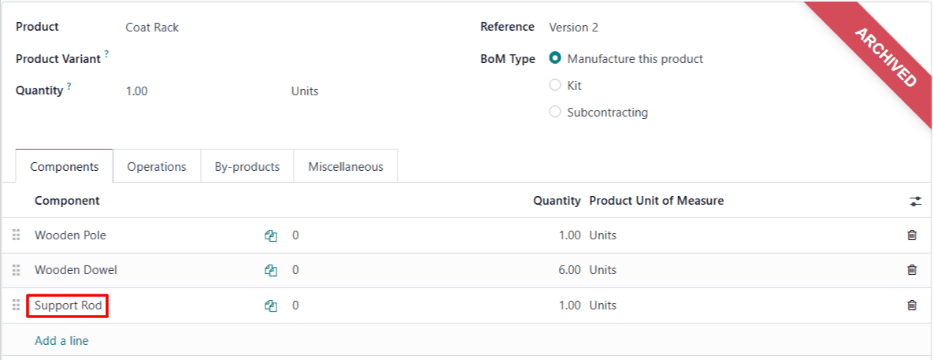
Jose reviews the changes, and confirms they are an effective method for addressing the problem with the coat rack. He moves the ECO to the Approved stage, which makes version two of the coat rack BoM the current version.
Now, each time an MO is created to produce a coat rack, the updated BoM is automatically selected. Wood Hut begins producing the improved coat rack, and customer feedback confirms that the new version has addressed the problem with its predecessor.
Using the Odoo platform, Wood Hut has implemented an end-to-end product improvement process. Since the essential elements of this process (customer feedback, quality control, etc.) are always functioning, it can be reused to continuously update products and processes.